How we contributed to a freeze-drying process that is 20% faster than current methodologies.
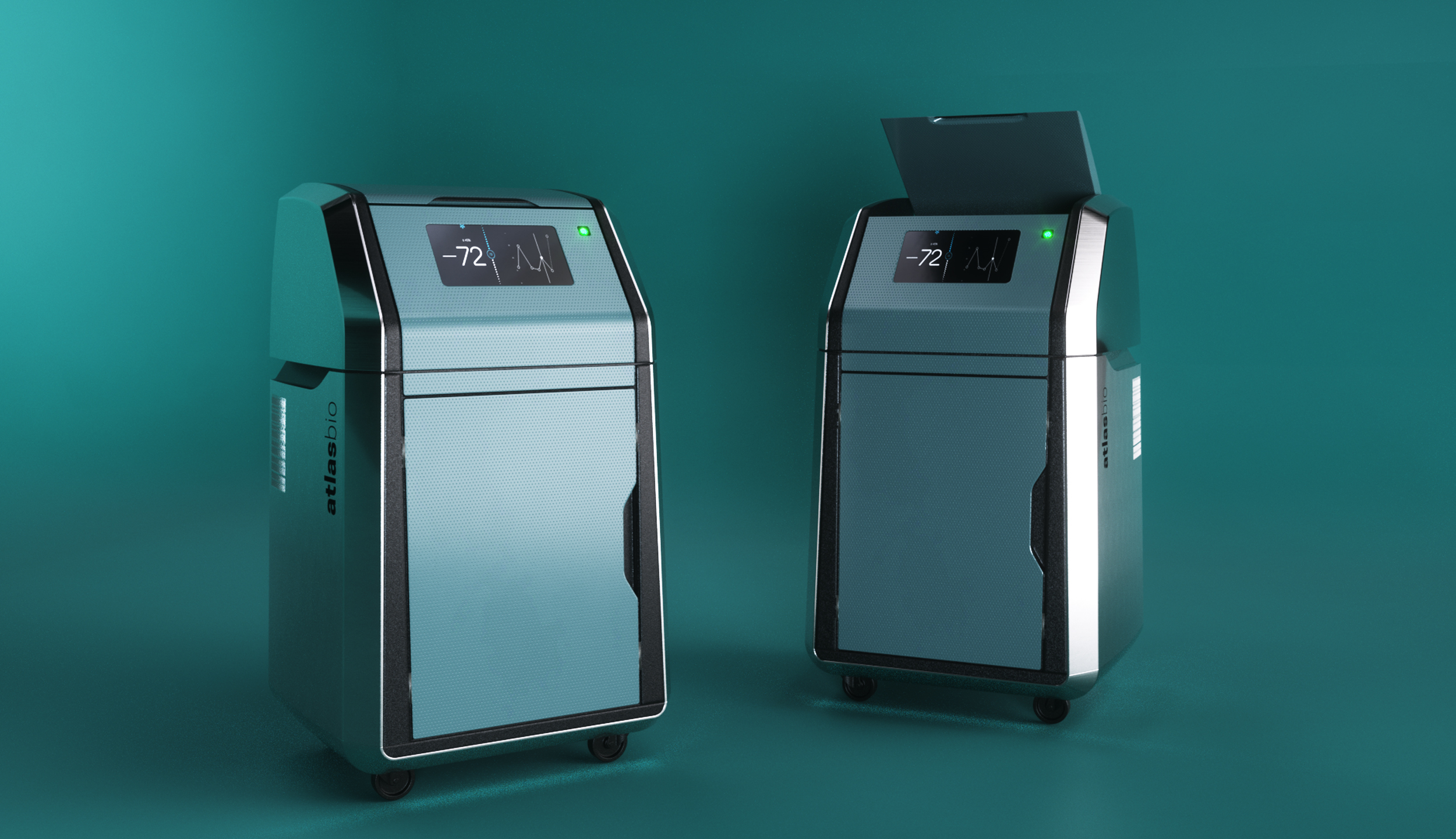
- GEA-Group
Sector
- Medical
Services
- Innovation
- Ideation
- Technology Research
- Technology Development
- Design
- Mechanical Engineering
- Detail Design
- Prototyping
Project
- Laboratory Scale Freeze Drier Range
A three-year research and development programme to design a laboratory freeze drier range incorporating Through Vial Impedance Spectroscopy.
GEA is one of the largest suppliers of manufacturing equipment for the pharma industry. This international technology group focuses on process technology and components for sophisticated production processes such as freeze-drying serving many end-user markets. In 2017 GEA generated consolidated revenues of about EUR 4.6 billion.
GEA are pioneers in continuous manufacturing (CM) solutions helping customers to develop, evaluate and optimise processing techniques to enable them to bring new products to market faster and cheaper. This project called for a range of small-scale freeze driers suitable for laboratory use to sit alongside their larger industrial driers.
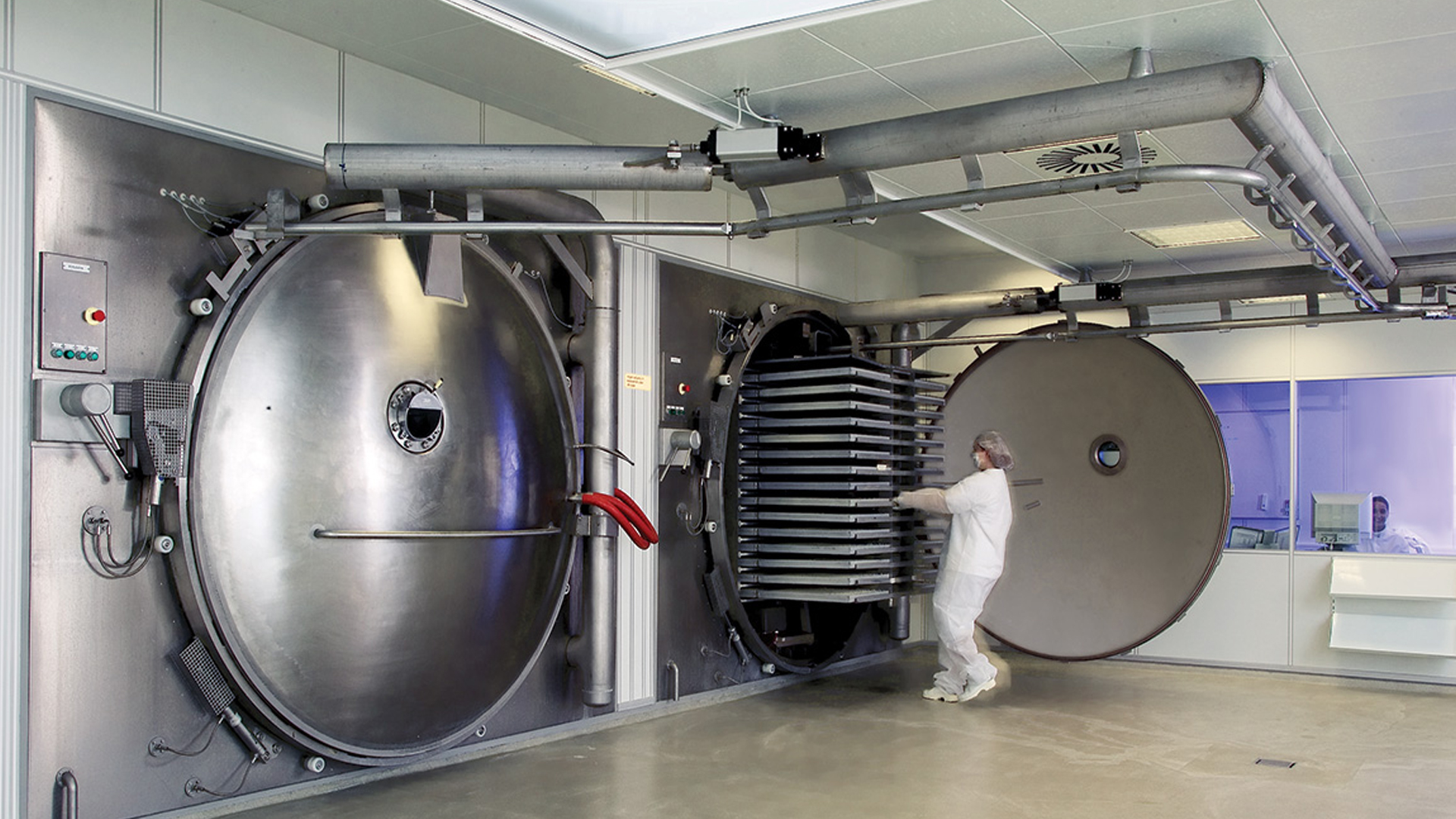
The Journey
A three-year research and development programme to design a laboratory freeze drier range incorporating Through Vial Impedance Spectroscopy (TVIS), enabling the formulation of room temperature stabilised biopharmaceutical products to deliver better designed and suited lyophilisation protocols. This patented GEA technology provides non-evasive real-time in-line monitoring of the process, leading to increased understanding and accelerated product development.
The challenge in this medical device design project was to develop a suitable freezing technology and engineer user-focussed laboratory equipment for benchtop and freestanding applications to support GEA’s industrial-scale freeze drier range.
Conventional freeze driers use a refrigerant gas to absorb heat along with condensers, vacuum pumps and control gear, the package is not suitable for miniaturisation. Following a technology review we developed and iterated through several phases a discrete thermo electric module and control system suitable for use in both the freeze (sublimation) and drying (lyophilisation) phases, capable of freezing to minus 55°c and drying to minus 80°c under vacuum of 0.05 millibar. Concurrent with this activity we miniaturised the TVIS sensor technology suitable for single use on 10 millilitre glass vials and defined a cost effective manufacturing process for these as well.
The Outcome
As a result of these activities we have designed and manufactured pre production systems for GEA to trial with industrial partners to pave the way for the adoption of this new technology. Current feedback demonstrates a 20% saving in the freeze-drying process compared to current methodologies increasing precision, optimising yield capability and enhancing drug safety.
Using this technology, products developed in the laboratory can now be scaled up for manufacture with confidence using identical protocols and formulations accelerating product development with more efficient manufacturing cycles.
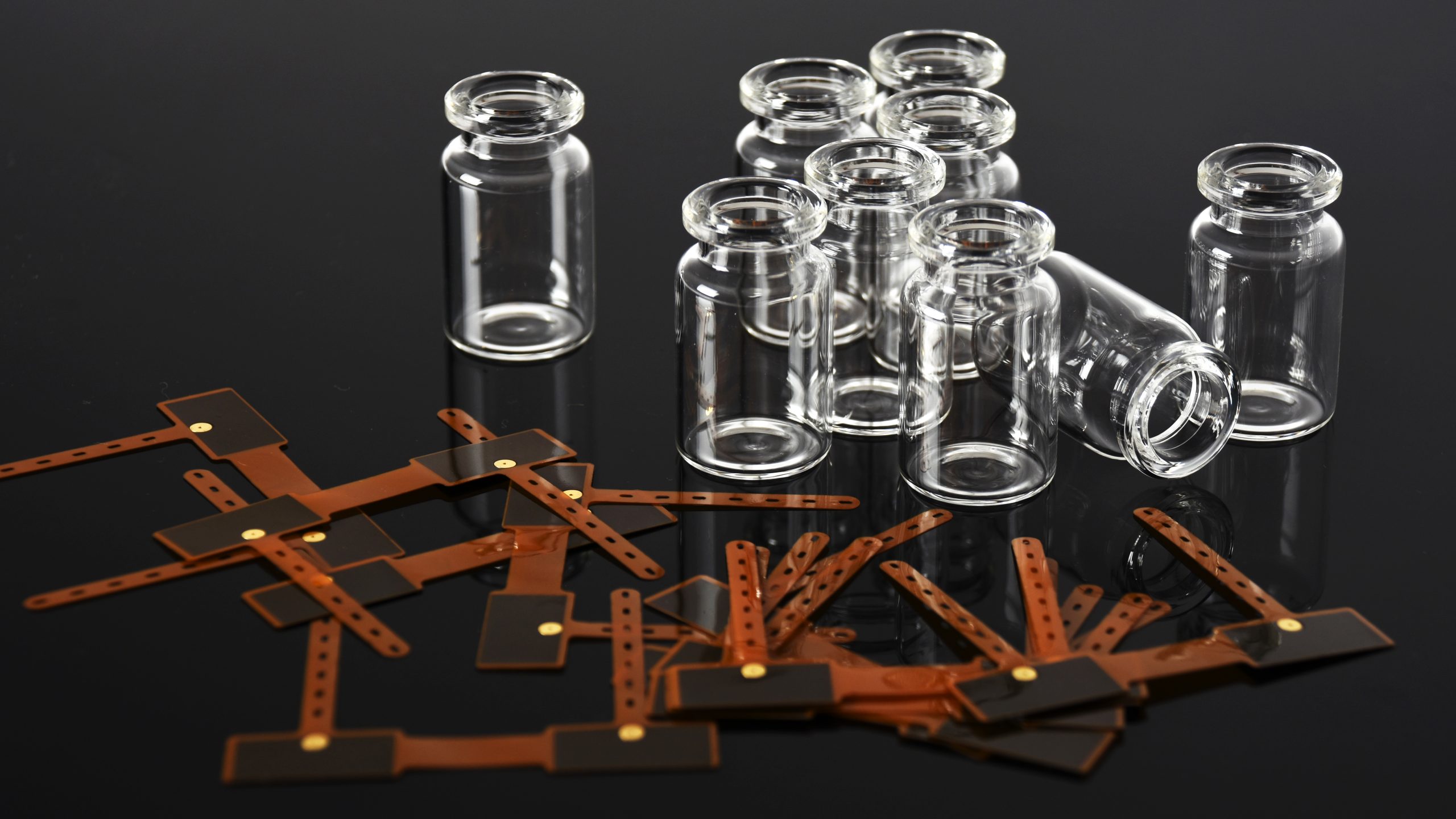