How to Reduce Manufacturing Costs with Smart Product Design
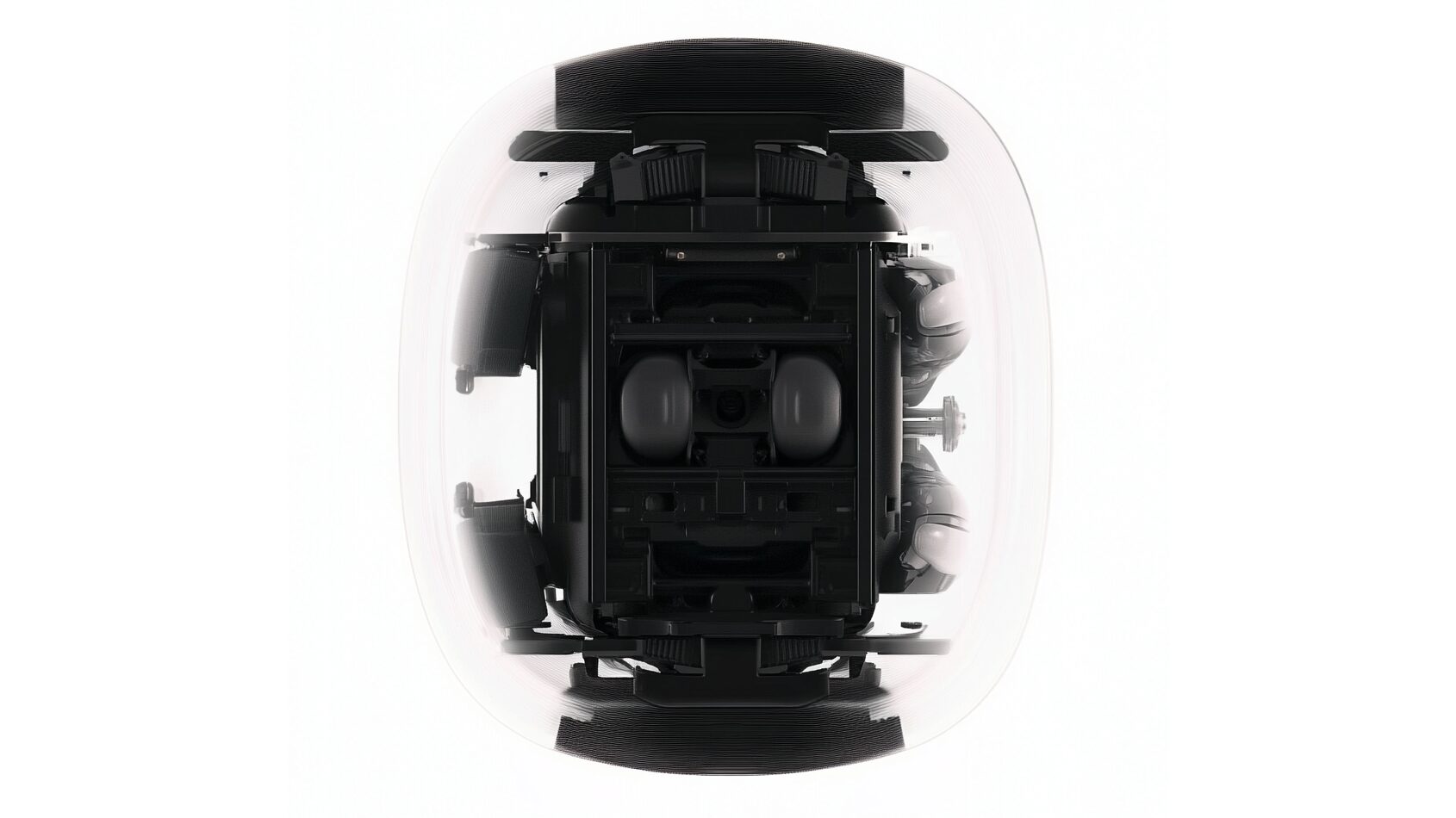
Looking to reduce manufacturing costs? Smart product design can help you achieve this. Cloud computing plays a crucial role in smart manufacturing by facilitating the collection and analysis of real-time data, which enhances efficiency and reduces waste. In this article, you’ll discover how to reduce manufacturing costs with smart product design by simplifying your designs, choosing cost-effective materials, and integrating automation to save money and improve efficiency.
Table of Contents
Key Takeaways
- Simplifying product design and reducing unique parts can lower manufacturing costs and enhance production efficiency.
- Optimising material selection and implementing Design for Manufacturability (DFM) can significantly reduce production costs while maintaining product quality.
- Engaging manufacturers and suppliers early in the design process fosters collaboration, streamlines production, and drives cost-saving innovations.
- Implementing these strategies can lead to greater cost savings by addressing various expenses, such as administrative and warehouse costs.
Simplify Product Design
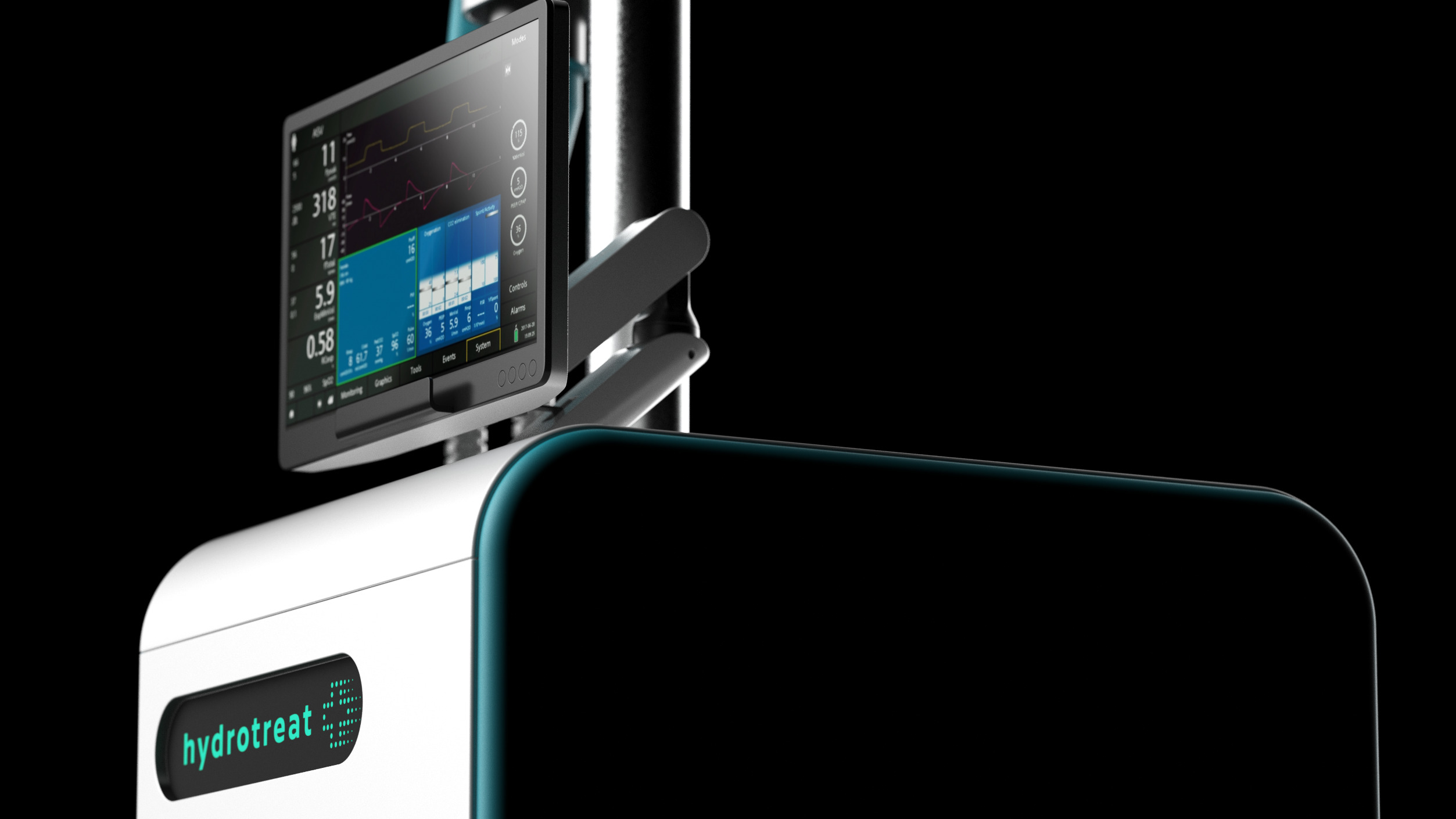
Simplifying product design can cut manufacturing costs by cutting costs through reducing parts, streamlining assembly processes, and minimising material usage. One of the most effective ways to achieve this is by reducing the number of unique parts in a product, which can lead to substantial savings in the manufacturing process. For instance, a consumer electronics firm managed to cut assembly time by 10% by redesigning its product to use fewer screws, resulting in substantial savings.
Standardizing parts not only simplifies the design but also saves valuable floor space, leading to reduced storage costs and improved organization.
Simplified designs often drastically cut assembly time, enhance efficiency, and reduce labor costs. This approach not only speeds up the production line but also reduces the chances of errors during assembly, leading to improved product quality. A systems approach to design allows for combining multiple mechanical parts into more efficient solutions, leading to a streamlined design.
Innovative design strategies can replace traditional components with simpler, more reliable alternatives, enhancing overall product functionality. This not only helps in reducing costs but also ensures that the product remains competitive in terms of performance and reliability. Decisions made during the product development design phase significantly impact the total cost of production, making it a crucial stage for implementing these changes.
Optimise Material Selection
Choosing cost-effective and readily available lightweight materials can lead to significant cost savings in the manufacturing process by reducing material costs. Evaluating material properties such as strength, flexibility, and thermal conductivity is vital for effective material selection. Considering these factors helps companies select alternative materials that meet performance requirements, minimise waste, and reduce overall costs.
Selecting cost-effective raw materials reduces raw material expenses, streamlines manufacturing, enhances durability, and improves supply chain efficiency. Strategically selecting materials can significantly lower the overall product cost while maintaining quality and performance. A holistic approach to material selection ensures a high-quality, cost-effective final product.
Implement Design for Manufacturability (DfM)
Design for Manufacturability (DFM) aims to align product design with manufacturing capabilities to lower production costs. This methodology focuses on designing products with manufacturing efficiency in mind, which can result in significant cost reduction, improved efficiency, reduced waste, and increased product quality. DfM can significantly lower manufacturing costs and time while maintaining quality and reducing overhead costs.
Engaging with DfM experts during the product development process can enhance efficiency, reduce costs, and improve product quality.
The choice of materials can directly influence manufacturing processes and overall product performance. Here are some key points to consider: 1. By selecting lighter materials, companies can enhance both manufacturing ease and product functionality. 2. Standardising components is another key aspect of Design for Manufacturing (DFM), leading to lower costs, quicker assembly, and less complexity in production. 3. Engaging suppliers early in the design process enhances risk identification and can lead to important factors such as better sourcing strategies and production timelines.
Collaborate with Manufacturers Early
Engaging manufacturers early in the design phase offers valuable insights. It can help identify manufacturability and cost-saving opportunities. By involving suppliers early, companies can identify cost-saving opportunities without sacrificing quality, ensuring that the final product meets high standards. Involving manufacturers from the start helps identify manufacturability issues and find alternative approaches to improve product design. Establishing strategic partnerships during the design phase ensures that the product is designed with manufacturing capabilities in mind, reducing potential costs and enhancing product quality.
Engaging manufacturers early in the design phase offers valuable insights, including:
- Identifying manufacturability and cost-saving opportunities
- Finding alternative approaches to improve product design
- Establishing strategic partnerships that ensure the product is designed with manufacturing capabilities in mind
Early collaboration often results in valuable recommendations that streamline production and reduce labor costs. This proactive approach aligns the design with the capabilities of the factory floor, enabling manufacturers to produce high-quality products more efficiently. The result is a well-designed product that meets market demands while minimising production costs.
Focus on Standard Components
Utilising standard components streamlines production and facilitates easier inventory management. By incorporating standard parts instead of custom-made components, companies can simplify product design and reduce the complexity of the supply chain. This approach not only makes procurement easier but also leads to significant cost savings and efficiency gains through enterprise resource planning.
Standard components enhance quality control by reducing variability in the production process, leading to enhanced quality and fewer defects. This consistency leads to higher product quality and fewer defects, ultimately reducing manufacturing costs. The use of modular design further supports this approach, as it allows for the easy interchangeability of components, leading to improved efficiency and cost reductions.
Incorporate Automation-Friendly Features
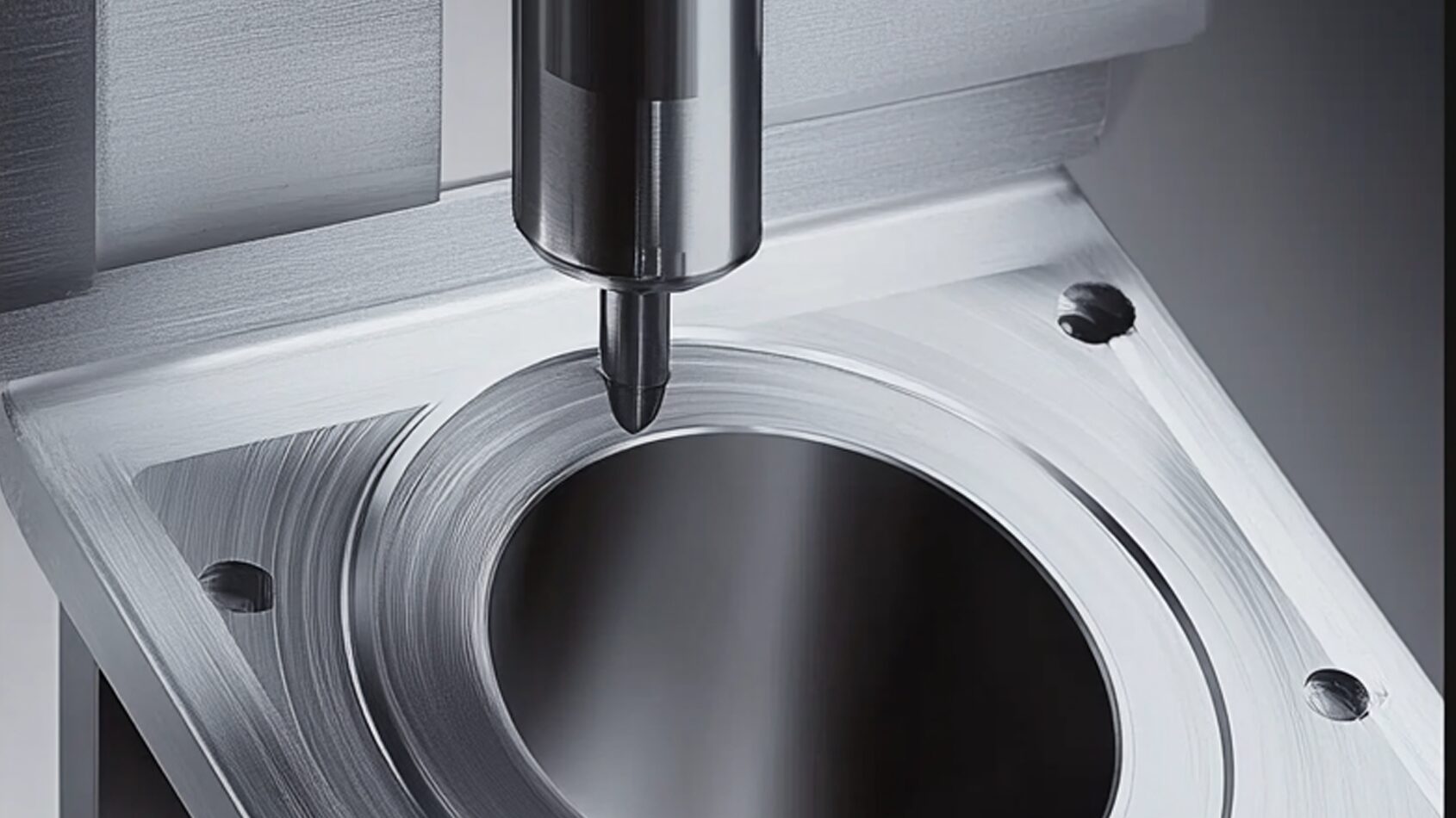
Designing products with automation in mind yields significant cost savings and increased efficiency. For a product to be compatible with automation, it must be suitable for machine handling and require minimal human intervention. Consistent and repeatable designs facilitate the use of robotics and automated assembly lines, thereby decreasing production costs. Implementing real-time data acquisition and visualisation is one effective method to reduce manufacturing costs through automation. Automation can significantly reduce costs by alleviating employees from repetitive tasks, allowing them to focus on more value-added activities.
Technologies such as OEE software can improve manufacturing operations and increase profit margins. Automated quality control in manufacturing reduces production costs, minimises human error, and improves inspection accuracy. Incorporating automation-friendly features into product designs leads to enhanced efficiency and cost savings across manufacturing processes. Advancements in technology, such as CAD software and 3D printing, facilitate the creation of physical prototypes, enabling designers to optimize models before full-scale production.
Embrace Modular Design
Modular design allows for the interchangeability of components, which can lead to economies of scale and simplified maintenance. Producing standard products can significantly reduce inventory carrying costs. For example, an automotive company reduced complexity and inventory needs by adopting a modular design approach, leading to significant cost reductions. This approach eliminates the need for forecasts or excess inventory, further decreasing operational expenses.
While maximum performance can be a goal, it is important to balance it with usability to avoid unnecessary expenses and ensure practical product development.
The design phase is critical for implementing modular design, as it allows for the creation of flexible and adaptable products that can be easily modified or updated without extensive retooling. This flexibility supports change management by enabling quick adjustments to the production line to meet evolving market demands.
Embracing modular design can also improve customer satisfaction by offering customisable options that meet individual preferences. This customisation capability allows companies to cater to a broader audience without significantly increasing production costs. The result is a versatile product line that can quickly adapt to market changes while maintaining cost efficiency.
Engage Suppliers Early
Engaging suppliers early in the design process ensures fewer time-consuming changes and aligns design with manufacturing capabilities. By involving suppliers from the beginning, companies can leverage their insights on materials and production processes, leading to significant cost reductions. Engaging suppliers early can lead to significant savings by leveraging their insights on materials and production processes, resulting in cost reductions. Suppliers can recommend the best parts that will be easily available, which assists in the product design process.
Good supplier relationships help secure the best prices on parts and products, enhancing cost efficiency. Collaboration with suppliers can speed up the time-to-market for new and improved products, giving companies a competitive edge. This proactive approach not only reduces production costs but also ensures the timely delivery of high-quality products.
Utilise Advanced Technologies
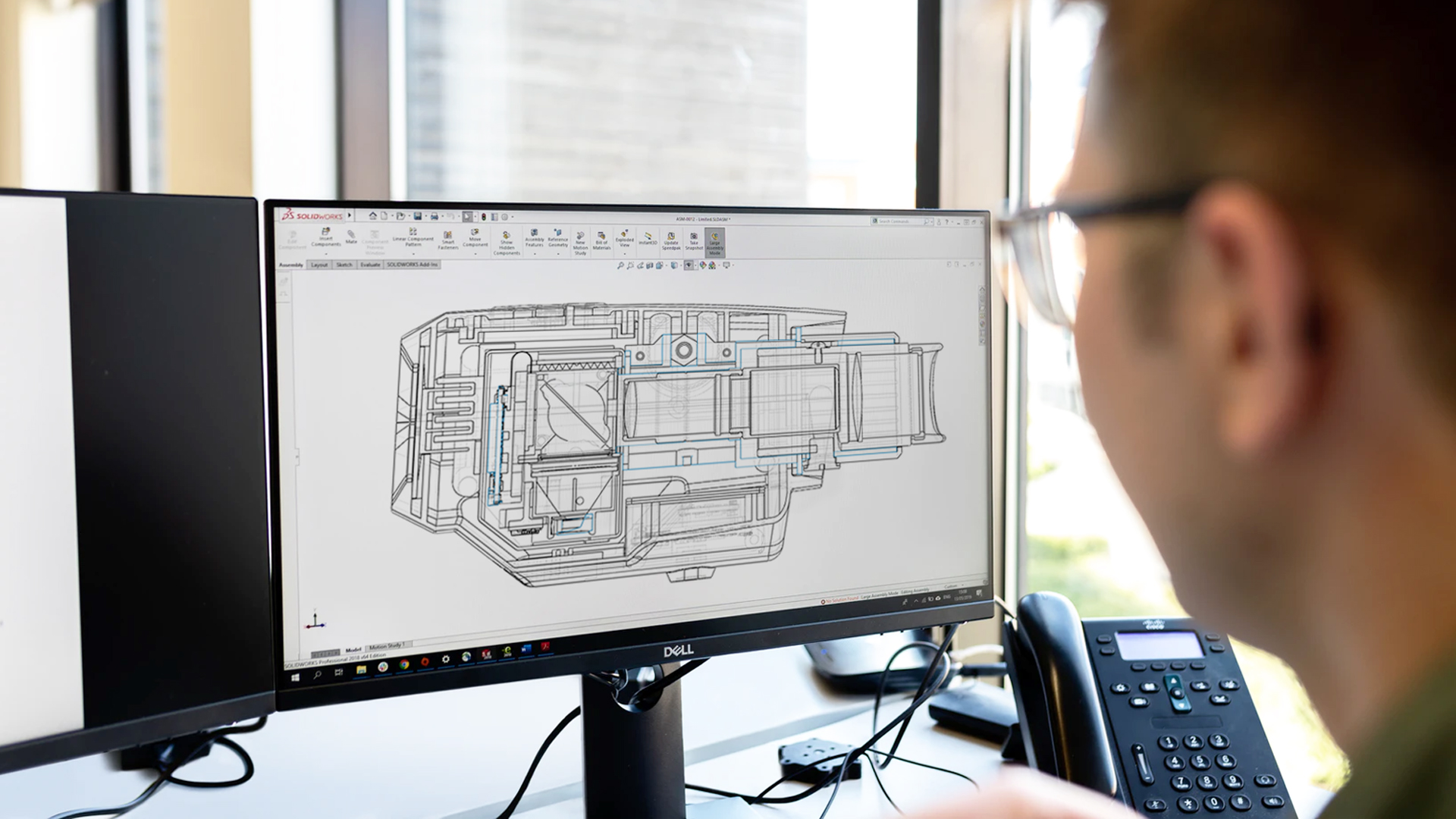
Technologies like CAD software and 3D printing are crucial for optimising design and reducing waste. CAD software supports the design process by enabling precise geometry editing and the creation of complex models that can be 3D printed. Additive manufacturing, commonly known as 3D printing, allows for the creation of objects by layering materials based on digital designs, leading to reduced material waste.
Technologies like CAD software and 3D printing help minimize waste by enabling precise design and efficient material usage.
3D printing technology facilitates on-demand production, allowing manufacturers to create parts as needed without extensive setup or tooling. Simulation tools help in optimizing designs before actual production, ensuring better performance and reducing the likelihood of costly errors. Digital platforms assist in selecting materials by comparing properties, costs, and processing options.
The integration of AI with digital twins allows manufacturers to monitor, analyse, and optimise production processes in real-time. AI-powered digital twins are essential for predictive maintenance, forecasting equipment failures before they occur. These technologies provide valuable insights through data analytics that enhance manufacturing operations and increase profit margins.
Design for Energy Efficiency
Traditional manufacturing is linked to high energy consumption and waste generation. Additionally, it contributes to significant greenhouse gas emissions, impacting the environment. By designing products for energy efficiency, companies can achieve significant cost savings and reduce their environmental footprint. Designing for energy efficiency not only reduces environmental impact but also leads to lower cost production by minimizing energy consumption. Switching to low-energy lighting and maximising natural light can help reduce energy costs in the manufacturing industry.
Smart manufacturing practices can reduce energy consumption, reduce waste, and greenhouse gas emissions. Regular good maintenance of manufacturing equipment is crucial for reducing energy usage. Designing products for disassembly and recycling reduces environmental impact and resource consumption, aligning with sustainability goals and lean manufacturing techniques.
Future Trends in Smart Product Design
The future of manufacturing may see the rise of autonomous factories where AI-driven systems self-optimise and reduce the need for human intervention. Modern manufacturing processes leverage artificial intelligence and machine learning for predictive maintenance, enhancing operational efficiency and reducing downtime. The integration of AI with digital twins allows manufacturers to monitor, analyse, and optimise production processes in real-time.
Technological advancements such as AI-driven systems and digital twins are expected to significantly reduce manufacturing cost by optimizing production processes.
Emerging technologies such as 5G will enhance the capabilities of digital twin by enabling faster data processing and real-time analysis. The modular approach allows for rapid adaptation to market demands, as manufacturers can easily modify future products by rearranging or updating modules. These trends will shape the future of smart product development, enabling companies to stay competitive in an ever-evolving market.
Summary
In summary, reducing manufacturing costs through smart product design involves a combination of strategies, from simplifying product design to leveraging advanced technologies. By optimising material selection, implementing DfM, and incorporating automation-friendly features, companies can achieve significant cost savings and enhance production efficiency. By implementing these strategies, companies can also reduce overhead costs, further contributing to overall cost savings. Engaging suppliers early and embracing modular design further contribute to cost reduction and improved product quality.
The future of smart product design is promising, with emerging technologies like AI-driven systems and digital twins leading the way. By staying ahead of these trends, companies can continue to innovate and remain competitive in the market. Embrace these strategies and watch your manufacturing costs decrease while maintaining high product quality.
View more of our Product Development Services
If you would like to hear more on how we can improve the quality of your products or help with your product development, please contact Bluefrog Design at mail@bluefrogdesign.co.uk
FAQs
How can simplifying product design reduce manufacturing costs?
Simplifying product design effectively reduces manufacturing costs by minimising the number of parts, streamlining assembly processes, and decreasing material usage. This approach not only lowers production expenses but also enhances efficiency.
Why is it important to engage suppliers early in the design process?
Engaging suppliers early in the design process is crucial as it aligns product design with manufacturing capabilities, resulting in cost reductions and enhanced production efficiency. This collaboration ultimately facilitates a smoother transition from design to production.
What are the benefits of using standard components in manufacturing?
Utilising standard components in manufacturing enhances production efficiency, simplifies inventory control, and decreases supply chain complications, ultimately resulting in substantial cost savings.
How does modular design contribute to cost reduction?
Modular design significantly reduces costs by enabling interchangeable components that lower inventory carrying costs and simplify maintenance. This approach streamlines production and operational efficiency, ultimately resulting in savings.
What role do advanced technologies play in reducing manufacturing costs?
Advanced technologies such as CAD, 3D printing, and AI-driven digital twins significantly lower manufacturing costs by optimising design processes, minimising waste, and improving efficiency. Implementing these innovations can lead to substantial cost savings for manufacturers.