Top Tips on How to Overcome Common Challenges in Custom Enclosure Design
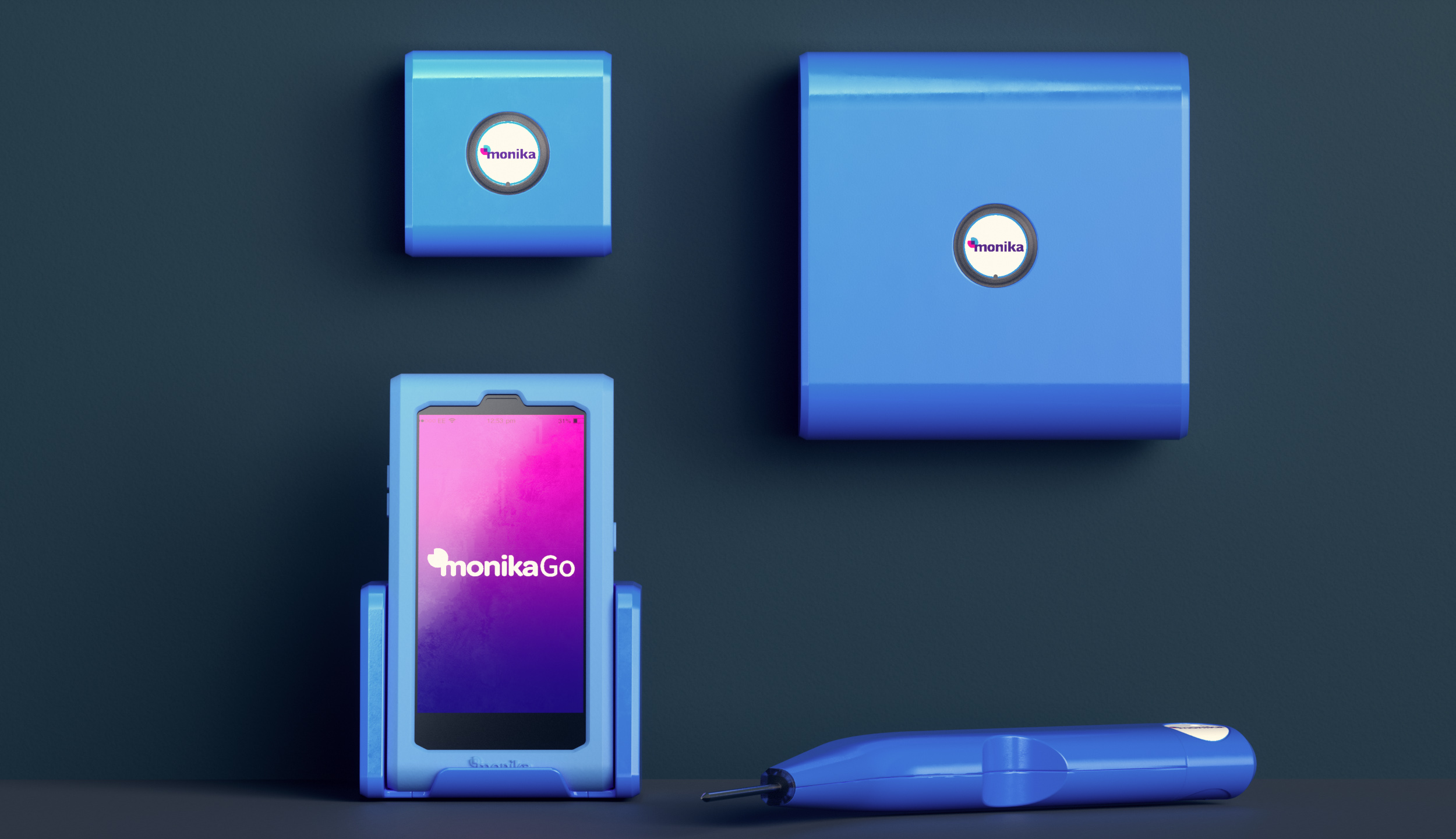
Struggling with common challenges in custom enclosure design? This article provides practical tips on how to overcome common challenges in custom enclosure design, including understanding client needs, balancing aesthetics and functionality, selecting materials, managing heat dissipation, and ensuring structural integrity.
Table of Contents
Key Takeaways
- A thorough understanding of client requirements is essential for effective custom enclosure design, ensuring alignment with functionality, aesthetics, and regulatory standards.
- Material selection plays a crucial role in the durability and performance of custom enclosures, necessitating careful consideration of factors like corrosion resistance and heat dissipation.
- Effective communication with manufacturers is vital throughout the custom enclosure design and production process to ensure collaboration, clarity, and adherence to specifications.
Understanding Client Requirements
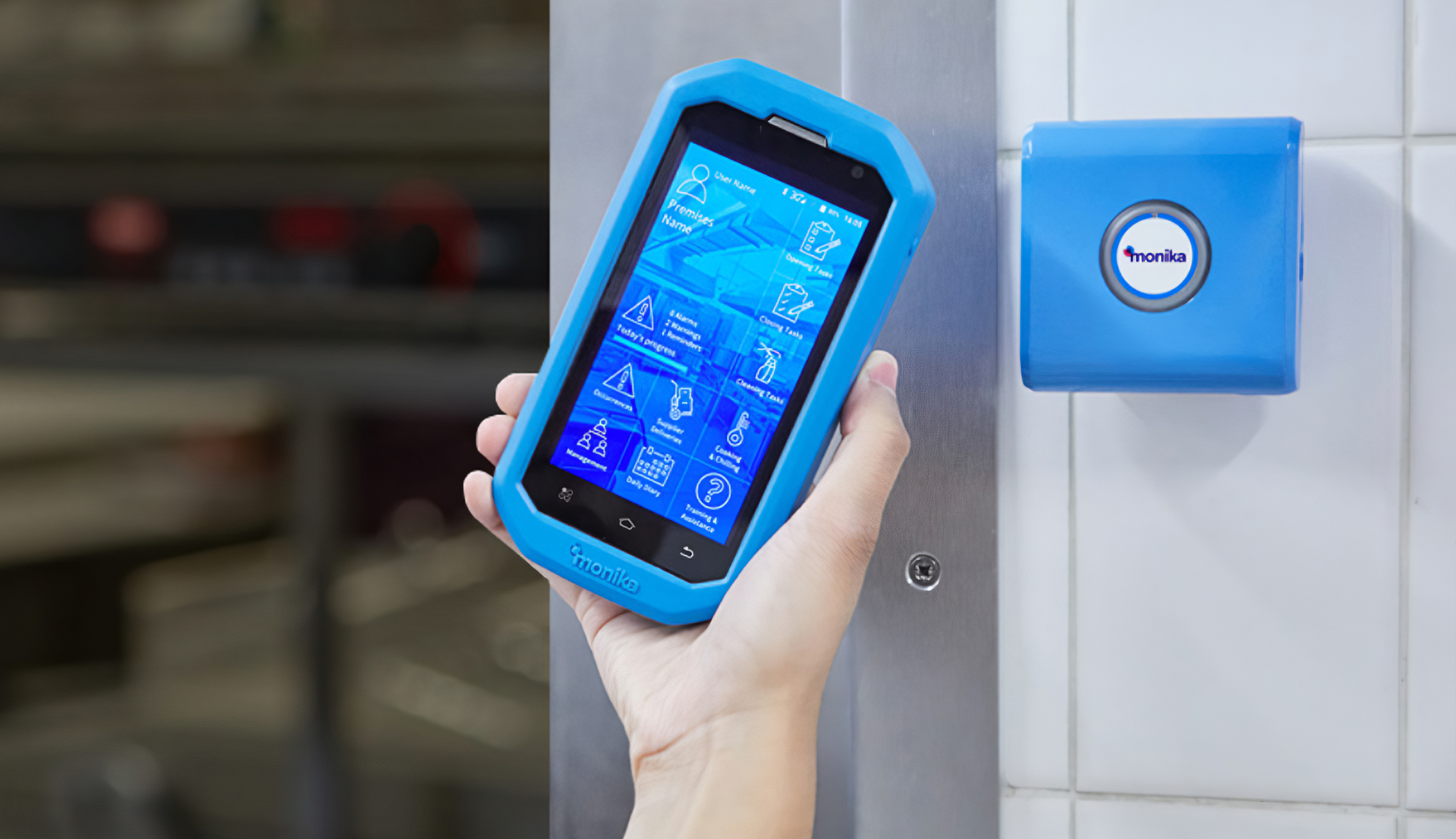
The foundation of any successful custom enclosure design begins with a deep understanding of client requirements. This initial phase sets the tone for the entire project. Custom enclosures are tailored from the ground up to meet specific project needs, rather than using generic solutions. This involves defining product requirements to ensure the enclosure aligns with functionality and regulatory standards.
Collaboration during the design phases ensures all client specifications are accurately reflected in the final product. This includes aspects such as easy access for maintenance, cable management, and a sleek professional design. Maintaining open communication and close collaboration with clients helps designers meet specific requirements and achieve expected performance in real-world conditions.
Moreover, custom enclosures can integrate branding elements, such as logos, to enhance product recognition. This not only meets the client’s specific needs but also helps in creating a cohesive brand identity. Documenting specific requirements early in the design process saves considerable time and resources later on.
Balancing Aesthetics and Functionality
Balancing aesthetics and functionality is crucial in designing enclosures. A well-designed custom enclosure must look good and ensure optimal performance. Achieving this balance begins with thoroughly understanding client needs and specifications. The design team must consider various shapes, sizes, and installation details to ensure that the enclosure meets both aesthetic and functional requirements.
Industrial designers and engineers must collaborate to balance form and function effectively. For example, a sleek, professional design can include features like efficient heat dissipation and cable management. Practical functionality involves ensuring easy access for maintenance and proper ventilation. These factors are crucial for maintaining the high functionality of the enclosure while still meeting the client’s aesthetic preferences.
Choosing the right color is another vital consideration in the design phase. The color of the enclosure should complement the brand identity and attract the target audience. Metal finishing services improve the appearance of custom enclosures. They can also enhance their functionality. Through careful consideration of these elements, designers can create enclosures that are both visually appealing and highly functional.
Material Selection for Custom Enclosures
The choice of materials is pivotal in the custom enclosure design process. Material choice affects both the durability and aesthetics of the enclosure. Steel, for example, is often preferred for heavy-duty applications due to its strength and durability. On the other hand, aluminum is valued for being lightweight and resistant to corrosion, making it suitable for various applications.
Stainless steel enclosures are advantageous, especially where hygiene and corrosion resistance are critical. This makes them ideal for industries like food processing and medical equipment. Alluminum enclosures are also suitable for electronics as they provide good heat dissipation. Commonly used materials in custom enclosure fabrication include stainless steel, aluminum, and galvanised steel.
Plastic enclosures are also an option, particularly when UV resistance and thermal stability are needed. High-grade plastics and metals are essential in custom enclosure design. Selecting high-grade materials is essential for ensuring optimal performance across various environments. Finishing operations, such as painting or coating, provide corrosion resistance, improved appearance, and enhanced durability for custom enclosures.
The goal of careful material selection is to meet client needs and ensure durability. Designers must weigh the pros and cons of each material type to create the perfect enclosure that meets all project requirements.
Managing Heat Dissipation
Heat dissipation is a critical challenge in designing electronic enclosures. High temperatures can cause damage and system failures, making thermal management crucial. Cooling systems, including fans and heat sinks, are commonly employed to dissipate heat from electronic components.
Liquid cooling systems are more effective than traditional air cooling for high-performance applications. Additionally, using thermally conductive materials like copper or aluminum can enhance heat dissipation in electronics. Proper ventilation is crucial for safe operational temperatures in systems like data centers.
Customised parts can significantly improve heat management by allowing for ventilation and strategic component placement. Incorporating these features ensures the enclosure can handle the thermal demands of the electronic components.
Ensuring Structural Integrity
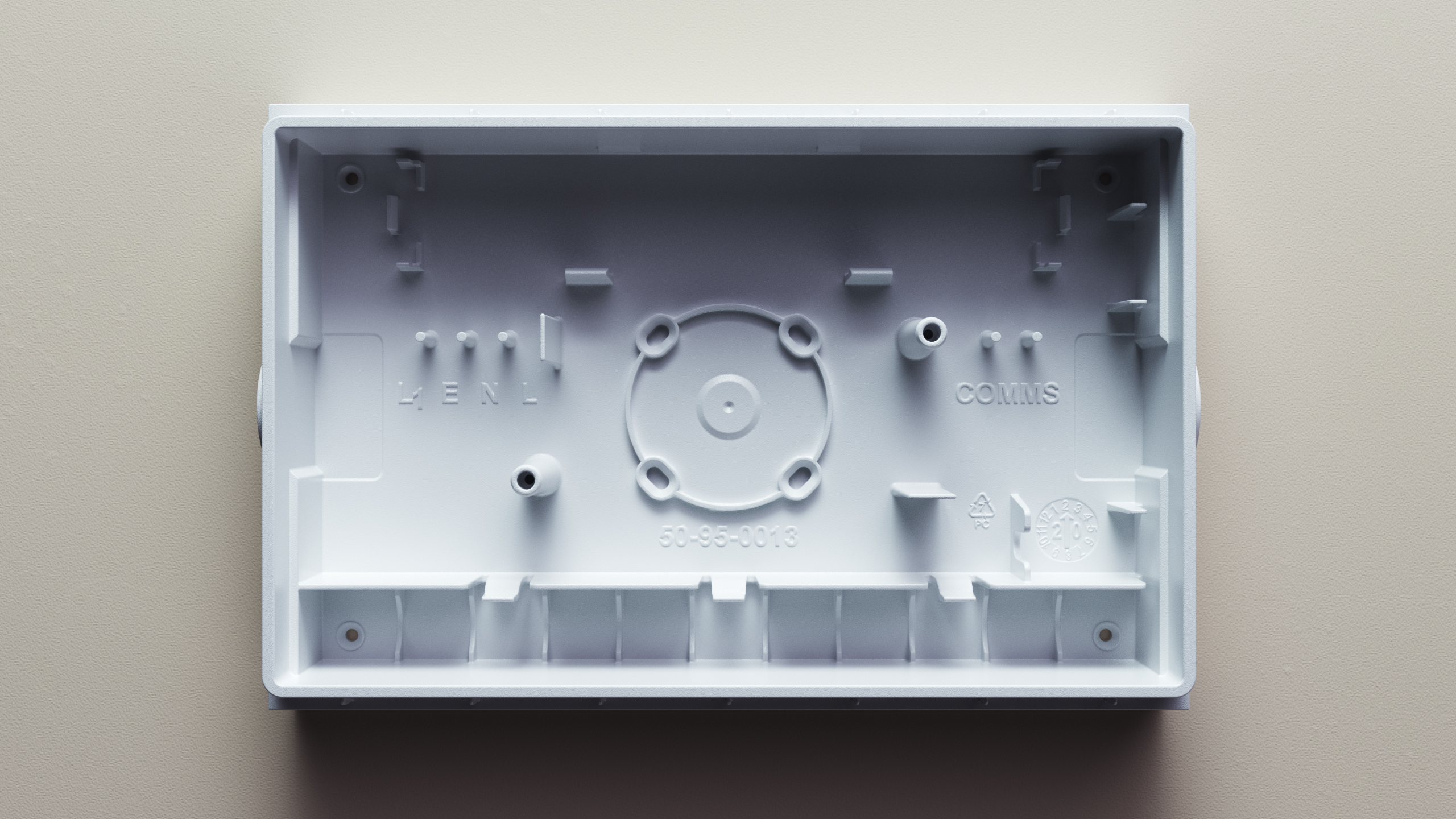
Structural integrity is vital in custom enclosure manufacturing to guarantee longevity and performance under stress. Precision sheet metal fabrication techniques significantly enhance the strength and rigidity of custom enclosures. This process involves meticulous attention to detail and precise tolerances to enhance structural stability.
Robust assembly processes prevent failures and ensure the enclosures withstand mechanical loads. This includes the use of high-quality materials and advanced fabrication techniques. Sealing mechanisms, such as gaskets or O-rings, are also essential for maintaining enclosure integrity in harsh conditions.
Focusing on these aspects allows designers to create enclosures that are strong, durable, and capable of protecting internal components from external stresses.
Protecting Internal Components
One primary purpose of custom enclosures is to protect internal components. Material choice impacts the enclosure’s durability and ability to protect against moisture, dust, and electromagnetic interference. Custom enclosures protect equipment from harsh conditions, damage, and unauthorised access.
Moisture, dust, dirt, heat, and physical impact can negatively affect electronic components. Custom enclosures shield electronic components from these potential threats. The design must adhere to industry standards like IP ratings for water and dust resistance.
Proper material selection and design ensure peak performance and reliability of electronic devices over time. This not only protects sensitive equipment but also ensures its functionality and longevity.
Prototyping and Testing
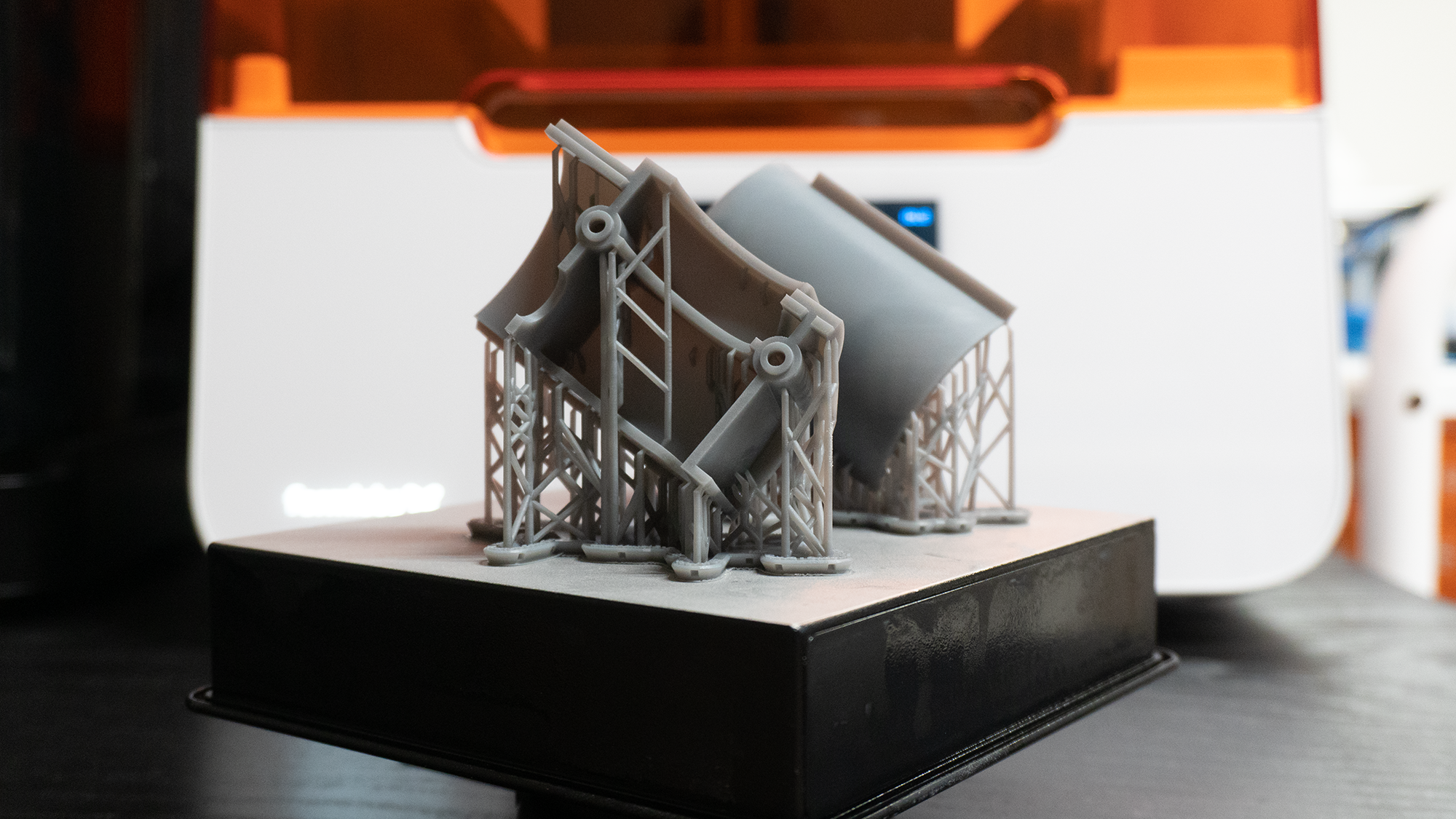
Prototyping and testing are crucial steps in the custom enclosure design phase. Prototyping helps identify design flaws early, saving time and resources in product development. Rapid prototyping and 3D printing are effective techniques for creating physical prototypes of custom enclosures.
Prototyping aims to test and refine the design. Validation testing confirms that the prototype functions as intended. Product design consultants facilitate iteration and adjustment based on client feedback.
Custom machining in the prototyping phase can save time and costs by identifying design flaws early. This ensures the final product meets specific requirements for optimal functionality.
Optimising for Mass Production
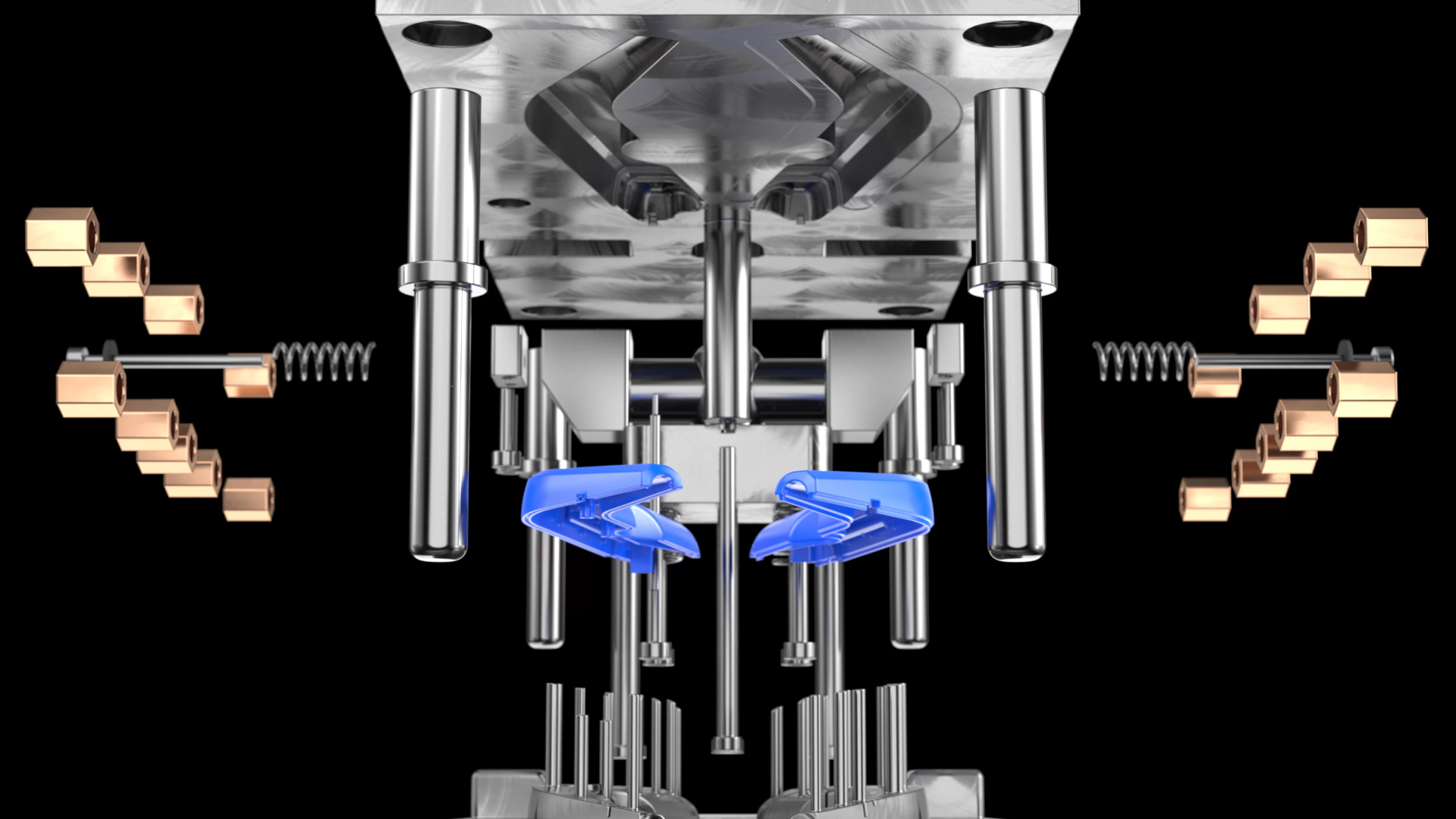
Optimising for mass production is crucial for creating enclosures that provide competitive market advantages. Custom machining enables precise and intricate designs, facilitating efficient mass production to manufacture custom enclosures. Using custom-machined parts enhances the fit and durability of enclosures, crucial for mass production.
Feedback loops with manufacturers are important; their input can improve both design and manufacturability. This ensures the final product meets required standards and is ready for mass production.
Effective Communication with Manufacturers
Effective communication with manufacturers is vital for a successful production process. Regular updates enhance collaboration and address potential issues early in the production process. Visual aids, like CAD drawings, clarify complex design details during discussions with manufacturers.
Documenting all communications and agreements provides a clear reference to prevent misunderstandings. Maintaining effective communication ensures the manufacturing process runs smoothly and the final product meets all specifications.
Summary
In summary, overcoming the common challenges in custom enclosure design requires a thorough understanding of client requirements, balancing aesthetics and functionality, careful material selection, effective heat dissipation management, ensuring structural integrity, and protecting internal components. Prototyping and testing, addressing environmental conditions, optimising for mass production, and effective communication with manufacturers are also critical.
By following these tips, designers can create custom enclosures that are durable, functional, and visually appealing. Embrace these challenges as opportunities to innovate and create products that stand out in the market.
View more of our Product Development Services
If you would like to hear more on how we can improve the quality of your products or help with your product development, please contact Bluefrog Design at mail@bluefrogdesign.co.uk
FAQ’s
Why is understanding client requirements crucial in custom enclosure design?
Understanding client requirements is crucial in custom enclosure design as it ensures the enclosure meets specific project needs and complies with functionality and regulatory standards. This alignment ultimately leads to client satisfaction and project success.
How can designers balance aesthetics and functionality in custom enclosures?
Designers achieve a balance between aesthetics and functionality in custom enclosures by collaborating closely with industrial designers and engineers, carefully considering practical needs, and thoughtfully selecting colours and finishes. This integrated approach ensures that both beauty and usability are effectively incorporated.
What materials are commonly used in custom enclosure design?
Stainless steel, aluminum, and high-grade plastics are commonly used in custom enclosure design, chosen for their durability, corrosion resistance, and suitability for specific applications.
Why is prototyping important in the custom enclosure design process?
Prototyping is crucial as it enables early identification of design flaws and ensures that the final product aligns with both functional and aesthetic requirements. This process ultimately saves time and resources.
How can effective communication with manufacturers improve the custom enclosure manufacturing process?
Effective communication with manufacturers enhances the custom enclosure manufacturing process by ensuring that design details are clearly understood and issues are addressed early, ultimately leading to a product that meets all specifications and standards.